3D printing Moulds for Carbon Fiber Parts
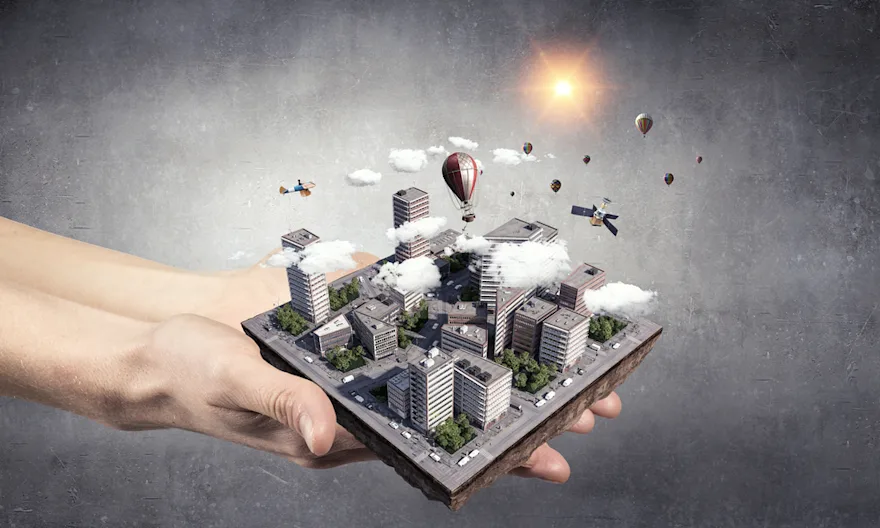
3D printing has come a long way in the last several years, reshaping the landscape of manufacturing by introducing the “additive” manufacturing process. The additive manufacturing process builds objects by adding material layer by layer, subtractive manufacturing, which Is the traditional method, is done via cutting / removing materials. This post will delve into how 3D printing is transforming specifically the mould making process for carbon fiber components, and the associated challenges that exist with this innovative approach.
The traditional Mould-Making Process:
Before moving further into the advantages of 3D printing, it’s important to understand the traditional approach to mould design and manufacturing. This process is not much different in either additive or subtractive processes, and the majority of the steps are not specific to carbon fiber, but would be required in design of any mould tool.
- Design and Prototyping: The initial mold design is often created using CAD software. Once the design is finalized, a physical prototype is typically made, often using materials like clay, foam, or even early-stage 3D printing.
- Mold Fabrication: The prototype is then used to create a mold, often through processes such as CNC machining or manual sculpting. This mold is usually made from metals, high-density plastics, or composite materials.
- Mold Testing and Adjustment: The mold is tested with a batch of carbon fiber, and adjustments may be needed to refine the final product.
This traditional method can be time consuming, expensive, and labour intensive. Especially when working with more complex geometry or class A surfaces and parts.
Enter in 3D Printing: A Game Changer
3D printing has introduced several key advantages that have a revolutionary impact to the approach of mould-making:
- Rapid Prototyping and Iteration:
- Speed: 3D printing allows for the rapid creation of prototypes. What used to take weeks or even months can now be accomplished in hours or days. This accelerated timeline is crucial for industries where time-to-market is a competitive advantage. - Cost Efficiency:
- Reduced Material Costs: Traditional molds often require expensive materials and specialized machining. With 3D printing, molds can be produced using cost-effective materials like resin or specialized high-temperature plastics.
- Lower Labor Costs: 3D printing minimizes the need for manual labor and complex machinery, further driving down the overall cost of mold production. - Improved Accuracy and Consistency:
- Precision: 3D printing offers high levels of precision and consistency in mold production. This ensures that carbon fiber parts are produced with tight tolerances and high quality.
- Reduced Human Error: The automated nature of 3D printing reduces the potential for human error, leading to more reliable and consistent mould outputs. - Complex Geometries and Customization:
- Intricate Designs: 3D printing enables the creation of highly complex and detailed mold geometries that would be difficult or impossible to achieve with traditional methods. This capability is particularly valuable for intricate carbon fiber parts that require precise detailing.
- Customization: Custom moulds for unique or low-volume carbon fiber parts can be produced with ease. This is especially useful in industries like aerospace and automotive, where bespoke components are often required.
Applications and Case Studies
The use of 3D-printed molds for carbon fiber parts has seen significant adoption in various industries:
- Aerospace: Companies in the aerospace sector use 3D-printed moulds to create lightweight, high-strength components. For instance, NASA has utilized 3D printing to produce complex molds for spacecraft parts, optimizing both performance and manufacturing efficiency.
- Automotive: In the automotive industry, 3D-printed molds are employed to manufacture custom carbon fiber components, such as aerodynamic parts and performance enhancements. This approach allows for rapid prototyping and small-batch production runs.
- Sports Equipment: The sports industry benefits from 3D-printed moulds for custom-designed carbon fiber sports gear, such as bicycle frames and golf clubs. These moulds enable precise customization and high-performance characteristics tailored to individual needs.
Challenges and Future Directions
While 3D printing offers numerous benefits, there are challenges to consider:
- Material Limitations: The choice of materials for 3D printing moulds can impact the final product. High-temperature resistance and durability are critical for carbon fiber molds, and ongoing advancements are needed to address these requirements.
- Size Constraints: Large molds may still present challenges due to size limitations of 3D printers. However, advancements in printer technology and modular design approaches are helping to overcome these obstacles.
- Surface Finish: Achieving a high-quality surface finish on 3D-printed molds may require additional post-processing steps to ensure optimal surface smoothness for carbon fiber layups.
The embracement of 3D printing into engineering processes outside of just prototyping, such as mould design and production for carbon fiber parts marks a significant advancement in manufacturing technology. By leveraging cost-efficiency, faster speed and design flexibility 3D printing can produce high performance components with great precision at reduced lead times. As technology continues to evolve, we can expect even more innovations and improvements to the technology which will continue to show positive advancement within the manufacturing industry.