The Critical Role of Design and Engineering in Composites Manufacturing
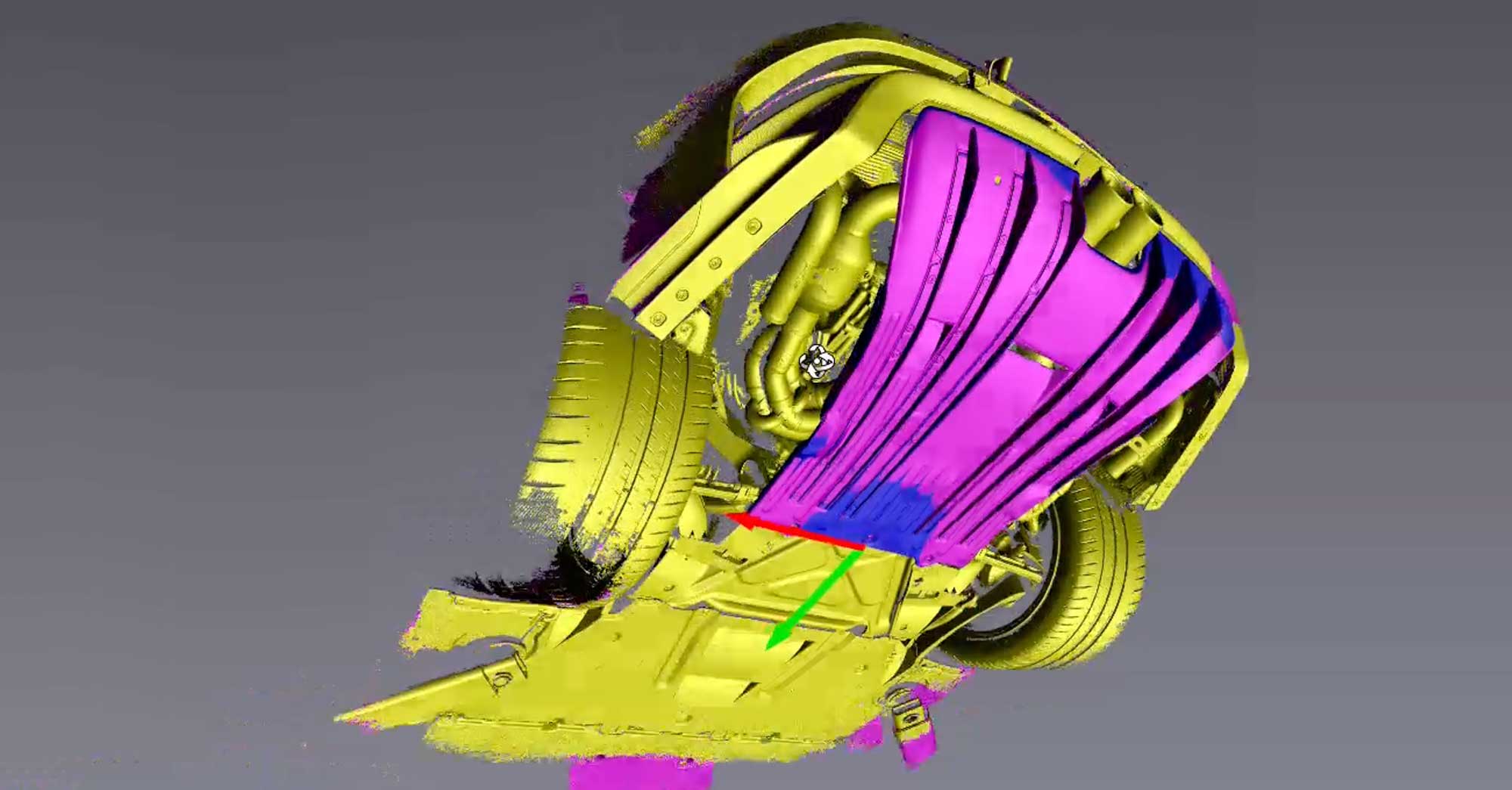
In today’s world of advanced manufacturing, composite materials are the gold standard for industries demanding strength, lightness, and durability. From aerospace and automotive to marine and industrial applications, composites are transforming how products are designed and built. But behind every high-performance component lies one essential foundation: smart, strategic design and engineering.
At Pfaff Technologies, we believe that engineering excellence starts long before the first fiber is laid. Here’s why the design and engineering phase is make-or-break for any composite project—and how it drives innovation, cost-efficiency, and long-term success.
Why Design and Engineering Matter
Unlike metals or plastics, composites offer a unique advantage: customization. Engineers can tailor mechanical properties to meet exact specifications. This flexibility opens the door to incredible performance—but also makes the design phase more complex and critical.
To achieve optimal results, every composite component must balance three key factors:
- Performance
- Cost
- Manufacturability
Let’s break down how expert design and engineering make it happen.
1. Material Selection & Optimization
Design begins with choosing the right materials for the job. This includes:
- Fiber types like carbon fiber, fiberglass, or aramid
- Resins and matrices such as epoxy, polyester, or thermoplastics
- Layup orientations to fine-tune strength, stiffness, and weight
A deep understanding of materials science allows engineers to push boundaries while staying within budget. It’s not just about using advanced materials—it’s about using them strategically.
2. CAD & Simulation-Driven Design
Innovation takes shape in CAD. Advanced software tools help engineers develop highly precise 3D models, laying the groundwork for success. But it doesn’t stop there.
Using Finite Element Analysis (FEA) and Computational Fluid Dynamics (CFD), we can simulate how materials will behave under stress, vibration, airflow, and more—long before a part is made. This predictive power helps optimize designs, eliminate weak points, and save valuable time in development.
3. Rapid Prototyping & Iterative Design
Speed matters—especially when you're racing toward the finish line. Our team uses rapid prototyping to test, tweak, and improve designs quickly:
- 3D printing with composite materials
- CNC-machined molds and tooling
- Small-batch resin infusion or prepreg layups
This fast, iterative process reduces both risk and cost while keeping your project on schedule.
4. Manufacturing-Ready from Day One
Great design is only great if it can be built. That’s why our engineers work hand-in-hand with manufacturing teams from the start. We plan for:
- The right layup and curing processes (vacuum infusion, autoclave, RTM, and more)
- Precision tooling and mold design
- Scalable production strategies
This integration ensures that every design is ready for real-world production without compromise.
5. Reverse Engineering for Innovation
Not every project starts from scratch. In many cases, the key to progress lies in the past.
Using 3D scanning and digital modeling, we can reverse engineer existing components to:
- Replace legacy parts when design files are unavailable
- Improve aging products with modern composites
- Reimagine high-performance systems in motorsports, aerospace, and restoration applications
It’s a powerful way to innovate by learning from what’s already proven.
Partner with Pfaff Technologies
Design and engineering aren’t just the first step in composites manufacturing—they’re the most important. At Pfaff Technologies, we combine deep technical knowledge with a hands-on approach to bring your ideas to life, faster and better.
Whether you’re creating a new product or improving an existing one, we’re here to help.
Contact us today to start your next project.